The discharge may be in a gas filled void in a solid insulating material, in a gas bubble in a liquid insulator, or around an electrode in a gas. When partial discharge occurs in a gas, it is usually known as corona.
Partial discharge is generally accepted as the predominant cause of long term degradation and eventual failure of electrical insulation. As a result, its measurement is standard procedure in the factory testing of many types of high voltage equipment. In addition, partial discharge activity can be tested for or monitored on in-service equipment to warn against pending insulation failure.
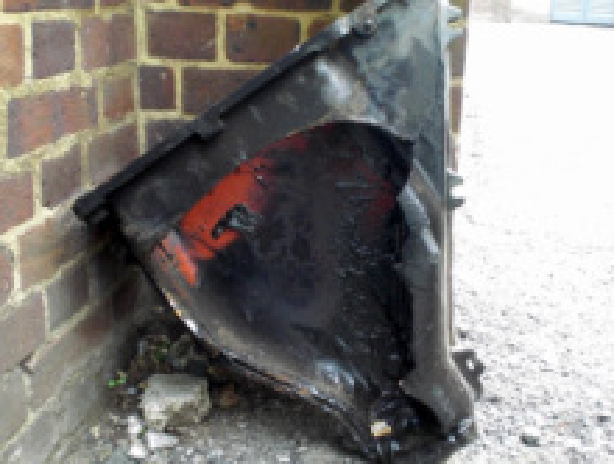
What is Partial Discharge?
How does Partial Discharge Occur?
Partial discharge occurs in gas filled cavities or defects in the high voltage insulation. These defects can originate in a number of ways;
During manufacture
Solid insulators are designed to give an even distribution of electrical stress between the conducting electrodes. However, in practice, defects can arise during manufacture that give rise to small cavities or voids in the insulation bulk.
Equipment installation
When electrical equipment is factory assembled or installed on site, mistakes can be made that either damage and therefore weaken the insulation, or cause increased electrical stress across the insulation.
Ageing and deterioration
Most insulating materials naturally deteriorate with age as internal chemical bonds break down. This process makes the insulation weaker and less durable when withstanding the electrical stresses arising under normal working conditions.
Over stressed in-service
A short circuit fault or lightening impulse is likely to impose stress on the insulation due to a fault current or an overvoltage. Although such events usually have a short duration, the increased electrical stress or heating from the current overload can cause permanent damage to the insulation.
In-service damage
Electrical equipment can be physically damaged whilst in service due to external factors. Underground cables are particularly susceptible to third party damage, by, for instance road works near buried cables or the cumulative effect of heavy vehicles passing over them.
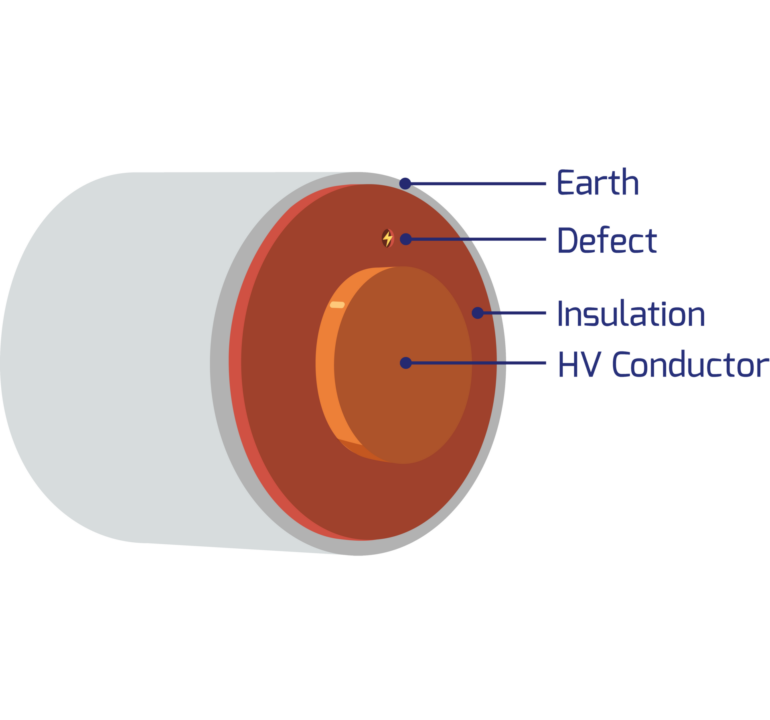
How to Detect Partial Discharge?
Why PD occurs at normal working voltages
The defects or cavities in solid insulation are usually filled with a gas of significantly lower breakdown strength than the surrounding material. In addition to this, the permittivity of the gas is invariably lower than that of the solid insulation, causing the electric field intensity in the cavity to be higher than that in the surrounding dielectric. Therefore, under the normal working stress of the insulation, the voltage across the cavity may exceed the breakdown value and initiate electrical breakdown, or Partial Discharge in the void.
Electrical power is generally transmitted with a sinusoidal alternating current. The insulation undergoes varying electrical stress throughout the power cycle, with two peaks in stress per cycle. This creates a very distinctive distribution of discharge activity. The pattern, or distribution of the discharges in the power cycle, is key to recognising PD and distinguishing it from other unrelated noise sources and identifying the source. The pattern is sometimes called a PRPD (Phase Resolved Partial Discharge) or φ-q-n pattern.
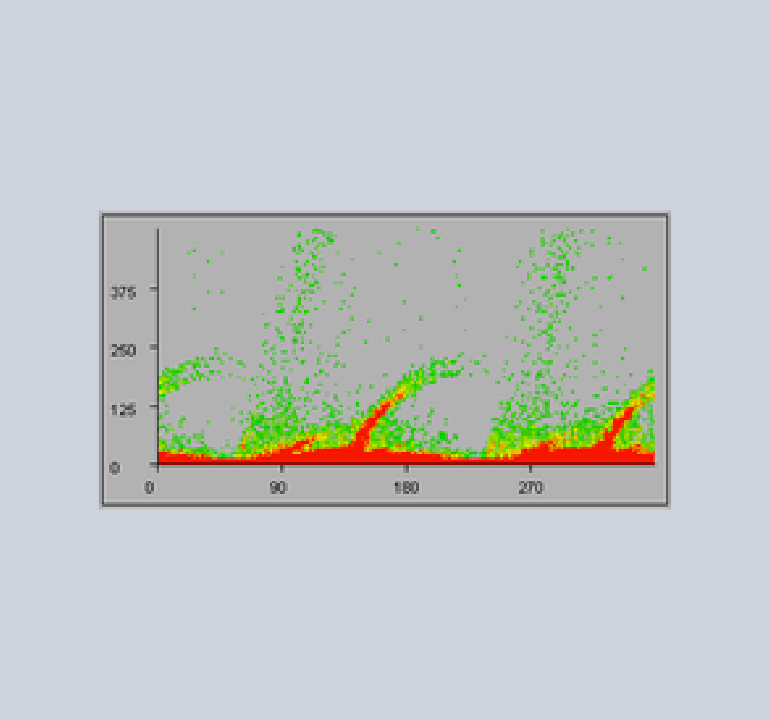
Surface Tracking
Tracking is the formation of a permanent conducting path across an insulator surface. Usually, the conduction path results from degradation of the insulation. Tracking occurs in carbon based compounds.
High voltage plants are often very difficult to clean and are therefore susceptible to dirt and contaminant can build up. In the presence of moisture, these contaminating layers give rise to leakage current over the insulator surface. This heats the surface and through evaporation causes interruption in the moisture film. Large potential differences are generated over the gaps in the moisture film and small sparks can bridge the gaps. Heat from the sparks causes carbonisation of the insulation and leads to the formation of permanent carbon tracks on the surface. Under such conditions, this process will develop over time and eventually lead to flashover and full breakdown of the insulation.
Tracking as a phenomenon severely limits the use of organic insulators in outdoor environments. The rate of tracking depends on the structure of the polymers and can be significantly reduced by adding appropriate fillers to the polymer, which inhibits carbonisation.
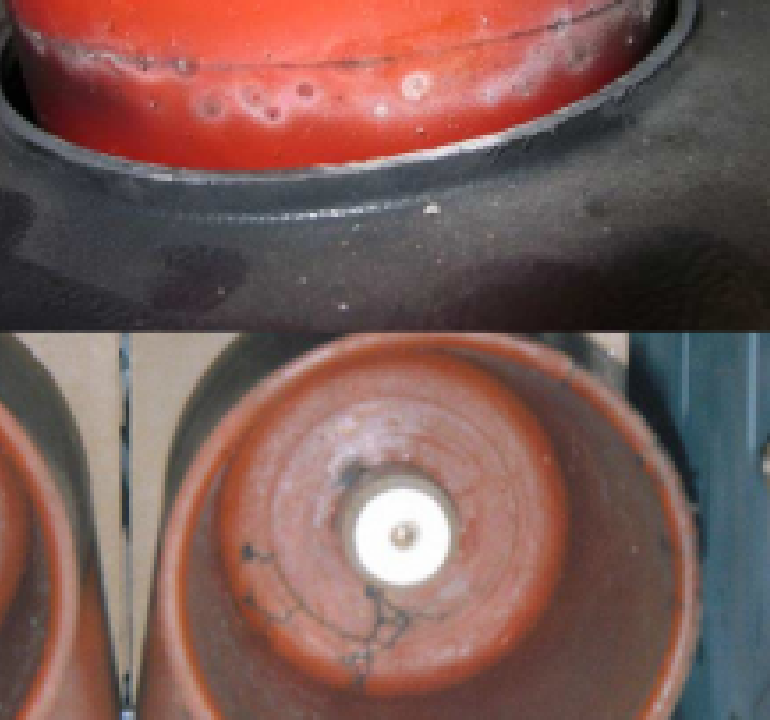
PD Testing and Monitoring Equipment
Research & Development
IPEC have a strong research and development team and as a result are able to offer test and monitoring solutions incorporating the latest technological advances with almost 20 years’ experience, IPEC has built a database containing over 400 million examples of Partial Discharge, all sampled at a high resolution from a wide range of HV assets. This unique data resource is used for the continuous development of PD detection algorithms; improving the accuracy and reliability of analysis. New products under development will make PD detection and location easier than ever before.
Contact