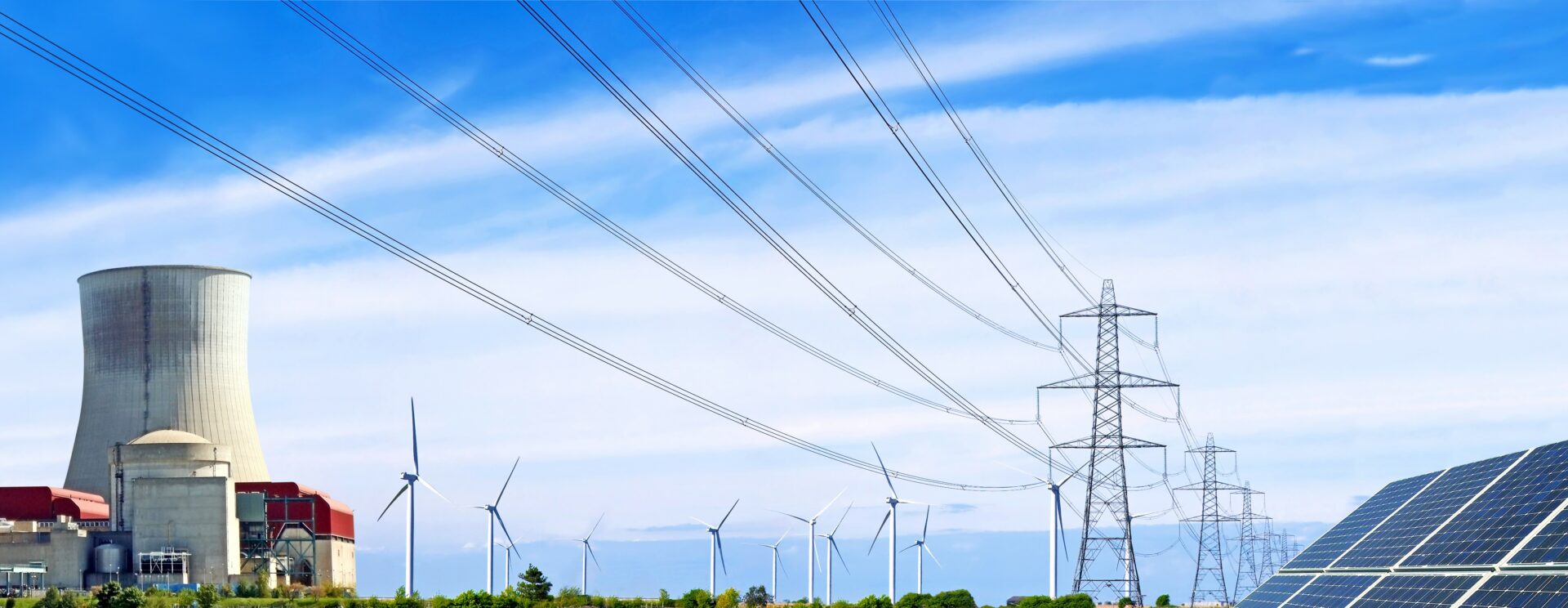
If Your Condition Monitoring is Failing to Deliver, Ask These Questions
10 / 05 / 19
Historically, time-based maintenance of assets was the predominant tool used to ensure asset managers optimise asset life and repair defects. Many industries now favour condition-based maintenance, as it allows asset managers to determine asset health, and often the nature and severity of a defect before failure occurs. Overall, this improves reliability, performance and importantly, reducing costs. Implementing condition monitoring is a complex and costly process with many considerations. To help you ensure that your efforts and costs deliver a return on investment, we’ve compiled a list (and infographic) of questions to ask if your condition monitoring is failing to deliver.
Are you compliant?
First and foremost, it’s essential that any condition monitoring implemented in your business is in line with internal and external technical standards. Keep yourself and your organisation familiar and compliant with new or updated industry or sector regulations. This will ensure that you are following best practices in your condition monitoring. Furthermore, not all systems are made the same. Research your industry counterparts to gain greater awareness of condition monitoring.
Are you using suitable condition indicators?
A condition indicator is an identifiable feature of the data captured from the asset which changes as the asset degrades. The key indicators of equipment health and longevity can vary greatly. This will depend on what parameters are being monitored on the asset. It’s important to select condition indicators that are relevant to your strategy and goals. For example, at IPEC we help utilities and industrial companies to detect and locate partial discharge in cables, switchgear, and accessories. As partial discharge is the main cause of long-term degradation and eventual failure of electrical insulation, our products and services are optimised to highlight these condition indicators across our customer’s assets.
Have you prioritised your assets?
Consider the worst-case scenario of asset failure versus the cost of condition monitoring and maintenance. Your most critical assets will likely require permanent and detailed monitoring. Identify and prioritise the assets whose failure would stop operation or pose a safety risk to your staff. It would also be wise to monitor assets that are costly or difficult to replace. However, not all assets need the same care. It may be more cost effective to implement a more reactive form of maintenance in some cases. For instance, a ‘run to failure’ approach is best for disposable or inexpensive assets.
Are you monitoring frequently enough?
If your condition monitoring is failing to deliver, it could be because you’re monitoring irregularly. Condition monitoring can be carried out either by spot testing or permanent monitoring, but is recommended that routine condition monitoring is carried out at least every 90 days on assets. Critical assets usually require more regular or possibly permanent monitoring that provides a weekly or daily view of asset health.
Are you being alerted in enough time?
You should be notified of problems with enough time for maintenance. Above all, the goal of condition-based maintenance is to monitor and identify upcoming issues or failure of equipment. Condition indicators should trigger maintenance so that work can be completed well before the asset fails or performance falls below the optimal level.
Are you analysing your data effectively?
The effectiveness of condition monitoring is determined not only by the quality of data, but the quality of data interpretation. Some condition indicators are straight forward to observe and can even be performed by automated systems. However, some require the help of highly skilled data analysts in order to spot trends and early warning signs of failure in a timely and proactive manner.
Are you following suggested solutions following data analysis?
Once condition data is collected and analysed, it’s crucial to act on this information. For this reason, only implement condition monitoring if you are prepared to take the necessary steps to avoid asset failure. An asset management process and flow should be created to ensure clear step by step actions to follow. This will ensure both effective and timely problem-solving.
Are you using the right diagnostic tools?
As condition monitoring technology evolves, methods of measuring condition indicators are becoming increasingly available to the market. However, it’s important to consider your budget, size of asset base and suitability to your system. Therefore, matching the right solution (or combination of solutions) to your assets is key to improving their operation and performance.
Here at IPEC, condition monitoring is what we do. Helping network operators manage their, often large, asset base through a combination of portable tools, permanent systems and services & support.
IPEC are experts in on-line partial discharge testing of MV and HV plants. We develop world-leading tools in the detection and location of PD in cables, switchgear and accessories. Get in touch to find out how IPEC can help with your specific condition monitoring requirements.